Sustainability > Engineering and Logistics Sustainability Efforts
Engineering and Logistics Sustainability Efforts
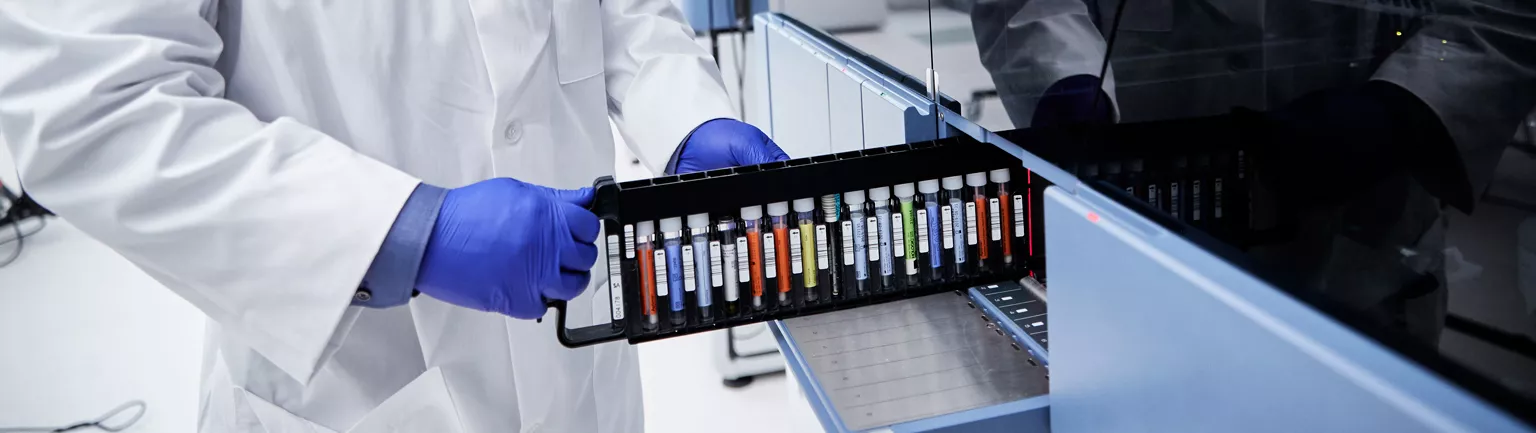
Hologic is committed to reducing our carbon footprint with headline environmental goals, as shown on page 35 of this year's sustainability report, and with efficiencies in our everyday operations.
Reusable Shipping Cases
Hologic's domestic suppliers of raw materials for the company's Diagnostic Solutions business use paperboard corrugated shipping cases to transport various plastic subcomponents that go into devices or hold the company’s reagents. In fiscal 2023, Hologic identified a process to implement reusable plastic corrugated shipping cases. These shipping cases will be flattened after use and returned to their manufacturer for inspection and reuse. This process helps to reduce Hologic’s carbon footprint by eliminating single-use paperboard corrugated shipping cases and the correlated transportation of single-use materials and waste.
Saving on Consumables in Diagnostics
Hologic’s Multiple Tiplet Unit (MTU) is a highly engineered plastic consumable required for the company’s Panther® instrument system. The previous pallet design contained 60 cases of MTUs for Panther. After a detailed analysis and ship testing verification, we determined that Hologic’s vendors can supply the company’s U.K. distribution warehouse with pallets that have 90 cases when shipping via ocean freight. With the additional material per pallet, Hologic can ship 1,800 cases per container compared to our previous shipping limit of 1,600 cases, an increase of 12.5%. This shipping efficiency has eliminated two full containers per month or 24 containers per year, reducing Hologic’s carbon footprint from air and ground transportation vehicles and the energy associated with that supply chain.
Ocean Freight Shipments
We have identified an opportunity to shift some of our shipping capacity from air and ground methods to ocean freight when distributing raw materials and finished goods. This process has eliminated emissions from tractor-trailers and airplanes that would otherwise be required to transport these materials. In addition to reducing our carbon footprint, we have also delivered financial savings of more than $1.5 million dollars through this process.